Given the disruptions in manufacturing over the past few years, companies have increased their focus on how to internally build more resilient supply chains.
Many dairy companies still rely on manual data entry and communication methods. This often results in errors, miscommunications and a lack of real time visibility into operations, all of which contribute to lost time and money. Mechanical breakdowns, maintenance requirements and unforeseen operational issues can lead to plant idle time, causing disruptions in the supply chain.
Turning to technology
For companies looking to automate their internal supply chain management, the question is how much and how fast. They may have automated some processes while others remain siloed and lagging in accuracy due to dated material and timed-out data.
Available technology can help capture data as it is generated, connect the data in a centralized view to create real-time visibility, said Sandeep Anand, senior director, decision science, Infor, New York. Anand was part of a panel at the International Dairy Foods Association Dairy Forum in Phoenix on Jan. 23, discussing how dairy companies leverage their businesses with evolving technology.
“When we talk about ‘the future is now,’ that’s true, because the technology has existed and the ability to monetize it, to build it into your business exists now,” he said. “The question becomes how do you start? Where do you see the value? How do you get your organization to evangelize it?”
Anand explained that when customers he works with at Infor ask what they are able to do with tools, such as machine learning, he often looks backwards. By looking at the end result a company wants to achieve, it’s easier for the company to start taking baby steps towards data-driven decision making.
“Generally, when you talk about machine learning, what kind of key benefits should you expect?” Anand asked. “Part of the value is that you do this in real-time so you can take the burden off of very experienced resources having to look at spreadsheets and being able to look at information that is, in some cases, quite complicated to make decisions when you’re in front of the customer. So, in supply chain, the value of near real-time decision making is to help you with margins. If you’re in the business of selling your goods, if you’re looking at it from a manufacturing perspective, of course you know asset maintenance … the machines you’re using are able to sustain the production output at the right quality, maybe even look at it from an efficiency perspective.”
Reducing downtime
In the world of dairy processing, efficiency is the name of the game. Any moment of inactivity, downtime or delays can lead to significant losses in terms of time and money.
Dairy supply chain software company Milk Moovement, Halifax, Nova Scotia, has a network that includes 2,500 dairy farms and more than 5,000 users. Per its data, the company manages more than 30 billion pounds of raw milk every year. Some of its partners include United Dairymen of Arizona and California Dairies Inc.
Idle time wastes valuable resources such as trucks, drivers and equipment. The underutilization of resources leads to inefficiency and higher operational costs. Extended idle time can also affect the quality and freshness of dairy products, especially in the case of raw milk. Delays in transportation can lead to spoilage or decreased shelf life. Unpredictable delays can disrupt delivery schedules, resulting in customer dissatisfaction and eroded trust.
The repercussions of plant idle time in the dairy supply chain also include financial loss. Fuel, labor costs and operational expenses continue to accrue while vehicles are stationary, which impacts the bottom line.
“After working at both the cooperative and plant levels of dairy I knew there had to be a better way to generate and share data to improve operations across the entire supply chain,” said Jon King, chief operating officer, Milk Moovement.
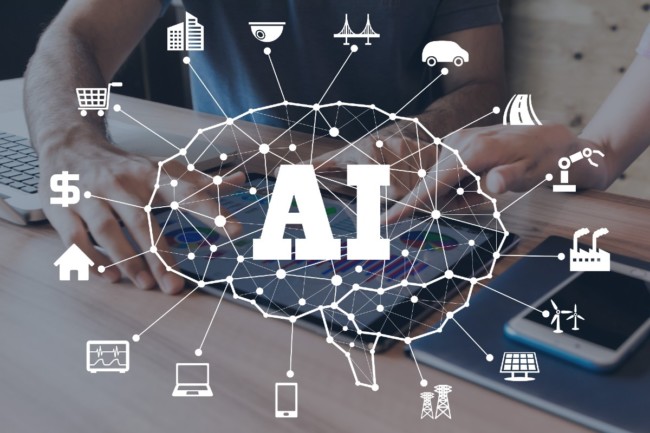
Artificial intelligence
Harnessing the power of artificial intelligence (AI) will be an important tool for manufacturers in the future, and those who begin exploring it now will have a leg up on competitors. AI can help increase the efficiency in manufacturing, improve quality control and create smart factories by connecting machines and systems with seamless operation and real-time data analysis and optimizing production processes.
Andy Lomasky, senior director of IT for PMMI, the Association for Packaging and Processing Technologies, urged companies to begin exploring this technology by trying it out in small ways.
“You don’t have to tackle connecting your entire shop floor to AI after a first go around,” he said. “Start learning. To me that’s the most important thing. Start with a small and simple use case and learn what it takes to make it a little better the next time. And make it iterative. Make it a process where you continuously learn and improve.”
Roambee, Santa Clara, Calif., a supply chain intelligence platform, is using AI to aid food supply chain companies.
The platform can predict quality compliance of shipments days before arrival at distribution centers or at stores, and the company said its solution can address challenges that come with food cold chain visibility.
“Roambee’s cutting-edge technology recognizes the importance of maintaining optimal conditions during the transportation of food and beverages,” said Sanjay Sharma, chief executive officer, Roambee. “Beyond the time-sensitive nature of these shipments, the susceptibility to contamination and the need for uncompromised quality are paramount. By providing real-time visibility and intelligent insights into the location and condition of food, Roambee not only enhances quality of delivery in the food industry, but also facilitates traceability, ensuring the origin of the product can be easily determined.”
Software and services supplier Ever.Ag, Frisco, Texas, revealed its newest solution makes use of artificial intelligence (AI) and machine learning to produce more effective cheese yields.
The company said it designed its newest program, Cheese Yield Optimization, to help cheese manufacturers maximize efficiency, reduce waste and increase profitability.
“What is exciting about Cheese Yield Optimization is it learns from existing and new data sets to highlight operational improvements, without taking away the ‘art’ of making cheese,” said Ryan Mertes, Ever.Ag’s head of manufacturing solutions. “The system does this with recommendations tailored to the user.”
Mertes said customers will receive results in as few as 90 days because the system uses existing data.
The AI assistance enhances decision-making at a cheese plant, leading to improved product consistency, quality and yield. The supplier said customers can use the technology to improve margins and bottom lines with yield improvements and undergrade reductions.
The company noted that its new technology also supports workforce transitions and knowledge retention “as younger employees take over plant management.”
Simon Drake, executive vice president of data science solutions for Ever.Ag, called the AI-driven solution a “game changer” for the cheese manufacturing industry.
“By integrating AI into cheese production, we’re enabling manufacturers to not only maintain but also elevate the quality and consistency of their products,” Drake said. “This technology represents a significant step forward in supporting the dairy industry’s move towards more sustainable and profitable practices, ensuring that the time-honored tradition of cheese making thrives in the modern era.”