Flow wrap is the most popular packaging format for chunk and sliced cheese products sold in stores today, and dairy processors continue to turn to flow wrap solutions for flexibility and versatility.
“(Flow wrap) is actually one of today’s most stringent and difficult applications, as packaging must perform reliably under high-speed converting processes, withstand abuse in the supply chain and protect the freshness and flavor of natural cheese,” said Travis Klug, dairy marketing manager for Amcor Flexibles North America.
An eye-catching look
One of the biggest advantages of flow wrap packaging is the flexibility it provides dairy processors in creating a range of packages through relatively easy adjustments in production, said Hugh Crouch, product manager for Harpak-ULMA, Taunton, Mass. This allows processors to deliver unique-looking products to retail customers and create additional consumer interest.
Klug said Amcor offers finishing technologies including matte, antiglare and tactile options to help its customers’ brands perform better and stand out on shelves while also delivering consistent operational performance.
“In addition to adding new and existing flavors to a product lineup, an enhanced look and feel of a brand’s packaging can help drive differentiation,” Klug said. “Finishing technologies including matte and antiglare printing continue to become more popular, especially with retail formats, including flow wrap for chunk, sliced and snack cheeses.”
The growth of snacking also is driving the way flow wrap is being used in the cheese market. According to the National Library of Medicine, snacks have become a staple of the American diet, accounting for nearly a quarter (22%) of total energy intake among adults. Currently, more than 90% of US adults report eating one or more snacks on any given day, with an average of between 1.2 and 3.0 snacking occurrences per day.
As a result, consumers are looking for portability and convenience in their snacking options, and more cheese snacks are being delivered to consumers in flow wrap packaging, Klug said. In the past, string and stick cheeses were often packaged in forming/non-forming films, but flow wrap films are now being used for a new format of cheese snacking that includes small, thin rectangular slices.
“Especially in times of inflation, cheese converters often are looking for automation opportunities in their production processes to become more efficient, reduce labor and control costs,” Klug said. “As compared to other formats like forming/non-forming or shrink bags, flow wrap for chunk, sliced and snack cheeses allows cheese converters to maximize their efficiencies by minimizing the manual efforts of placing the cheese on the packaging line, while also running at much higher speeds.”
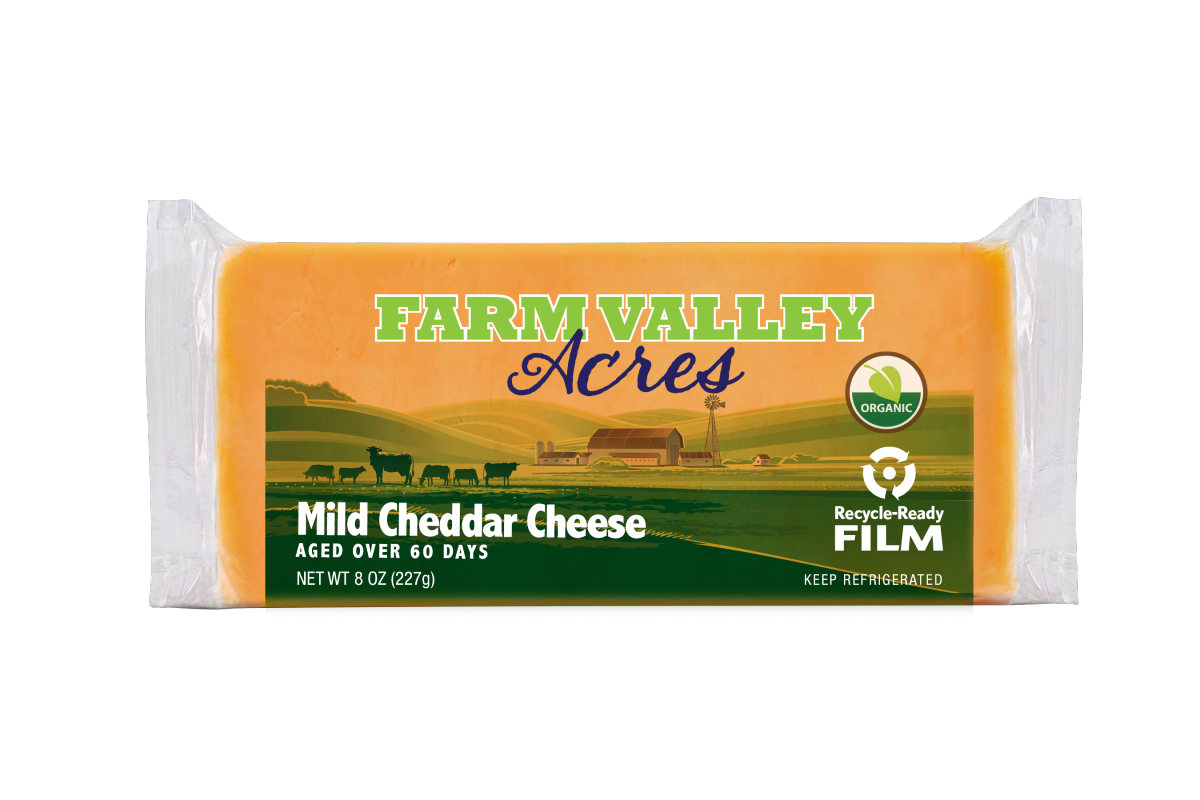
Amcor offers finishing technologies to help brands perform better and stand out on shelves.
| Image: AmcorFlow wrap solutions are also efficient in that they use only one roll of film, compared with tray sealing that requires a tray and top web of film, and thermoforming that requires two webs of film, Crouch said. Additionally, flow wrap requires no tooling and a smaller initial investment. Reduced changeover time is another benefit of such packaging, as film can be changed quickly, and machines can even perform automatic splicing.
Flow wrap offers higher production speeds for cheese products as opposed to others packaging formats, such as shrink bags and forming/non-forming films, Klug said. The flow wrap process also tends to be fully automated. In contrast, using shrink bags for chunk cheese is slower and could include some manual aspects.
Paxiom Group, Las Vegas, offers a variety of flow wrap solutions for dairy processors from entry level to high-speed with varying levels of robotics and automation including the Sleek i65 inverted flow wrapper designed for products like cheese that are more challenging to move.
Demand for flow wrap solutions is being driven by the need for scalability and automation to advance production while facing a challenging labor market, said Luis Pilonieta, director of sales for Paxiom Group.
“A brand is built on not only your product, but also the consistency that you can bring to the marketplace, from quality, to timing, to inventory across the supply chain,” Pilonieta said.
Processors are adding automation to ensure a reliable process that produces a consistent product, and flow wrap solutions are key to that consistency. Such a reliable process also helps lower the cost of production as automation allows companies to produce more units in the same amount of time.
Sustainable solutions
Flow wrap packaging enables processors to advance sustainability goals by reducing the amount of plastic used, Crouch said. He said Harpak-ULMA often develops solutions to replace a thermoform package with a flow wrap package to reduce total plastic.
According to the United States Department of Agriculture (USDA), the US alone discards between 30%-40% of the food supply. When cheese is packaged without enhanced protection, it is more likely that oxygen will enter the package or that the moisture levels will fluctuate, causing the product to spoil. Additionally, flexible packaging can aid in reducing a brand’s carbon emissions during transportation, because more can be transported at once, lessening the impact on the environment.
Crouch said there is a well-known wrap machine on the market that uses longer packaging for a block of cheese, but Harpak-ULMA has introduced a machine to reduce that packaging by 15 millimeters in length. While the resulting package might have a slightly different look, consumers were accepting in testing.
Amcor offers its AmPrima solution for recycle-ready flow wrap cheese packaging that is compatible with existing flow wrap equipment.
“(AmPrima) has heat resistance for operational excellence and maintains the same run speeds which is critical for this high-speed application. And it looks great, is abuse resistant and maintains high barrier – all things that are important for a package to ensure that the product is enjoyed by consumers,” Klug said.
Despite the successes in developing more sustainable packaging, achieving an ideal shelf life presents a challenge.
“Once you thin the film down and take some of the layers of the film out, then the modified atmosphere doesn’t last as long, because the breathability of the film changes,” Crouch said.
He said shelf life needs to be front and center in discussions around creating more sustainable packaging, because with reduced shelf life comes the possibility of creating more food waste.
“Do I reduce the shelf life of my product by using a more sustainable film or can I have a little bit thicker film and know that I’m extending the shelf life of that product, where I’m not… going to be throwing it away,” Crouch said.
Producing packaging machines with the highest level of flexibility in sealing is another important consideration, Crouch said. The industry learned during the pandemic that the supply chain can change quickly, leading to the use of many types of film structures.
Pilonieta echoed the importance of working with many types of film structures.
“There are hundreds, if not thousands, of different structures of film that can be used on a flow wrap machine, and the composition of those structures can really play a good determining point of successful production,” Pilonieta said. “There’s a never-ending search for a good combination to be more environmentally friendly.”
Making these combinations cost-effective is also important.
“There is a big interest and effort from both suppliers of equipment and suppliers of film to have a happy medium in which we can have a sustainable product from a film manufacturer that is going to be able to run on a piece of equipment that is still going to give you the results you are expecting and still be cost effective,” Pilonieta said.
Helping the dairy industry’s smaller producers scale and make production easier is a rewarding part of working in flow wrap, Pilonieta added. He said a small dairy farm the company worked with used a flow wrap solution, making it possible to bring its products to a wider audience.
Overall, delivering user-friendly solutions for operators with easy changeover and cleanability are areas that will drive innovation for flow-wrap technology in the future, he said. Ultrasonic sealing technologies are being tested in other industries, and this is a technology he thinks will also come to the dairy marketplace.
In the future, Harpak-ULMA plans to develop flow wrap packaging that can be reclosed and resealed, and Crouch said the company is anticipating what new film structures might come to the market.