Facing and managing risks is an inevitable part of doing business in any sector of manufacturing, and the way dairy processors approach the safety of both food and workers must also keep in mind the unique challenges of producing a product that must stay cold.
Additionally, cyber security threats must be taken seriously to avoid opportunistic attackers. As a result, processors are developing innovative ways of addressing each of these risks as the industry seeks to respond to challenges with resiliency.
Worker safety
Preventing injuries and promoting the well-being of employees is critical to minimizing risks in dairy processing. The top safety issues for workers at dairy processing plants are similar to those in other manufacturing sectors and include slips, trips and falls.
Procedures around the use of forklifts, machinery and energy and process safety management are also critical, said Danielle Quist, vice president of regulatory affairs and counsel for the International Dairy Foods Association (IDFA), Washington, DC.
While those potential hazards have been long-standing critical points of worker safety for the industry, Quist said new issues are also emerging. The training of temporary workers is now front and center, as the shortage of frontline workers has led to the use of many temporary workers.
Overall, Quist said increasingly companies are taking a more holistic and preventive approach to safety by using environmental health and safety management systems.
“There’s a belief that if you really use them consistently, and they’re championed across the company, they can result in fewer safety and environmental incidents and ultimately improve worker safety, health and welfare,” Quist said.
Safety regarding ammonia refrigeration is also a hot topic for processors, Quist said. While such refrigeration is being used more consistently because it results in lower greenhouse gas emissions, it also comes with a new set of safety considerations.
“Process safety management and ammonia refrigeration systems are heavily regulated, but they are also an important part of our industry’s ESG journey,” Quist said. “As we have a policy push away from using hydrofluorocarbons and moving toward the use of ammonia and natural, lower-emissions systems, the worker safety and environmental risks that follow are something our industry is going to have to pay more attention to.”
Employee engagement is also critical to preventing injuries, and involving hourly employees in discussions regarding reducing injuries is essential and more effective than corporate-driven initiatives, said Gregg Junck, senior manager for environment, health, safety and security for Le Mars, Iowa-based Wells Enterprises. In addition to slips, trips and falls, he said creating a workplace that promotes proper ergonomics is also important.
Hazards for potential injuries are especially prevalent for the dairy industry because the industry processes a product that must stay cold or frozen, leading many employees to rush and potentially make incorrect decisions for fear the product will spoil and cause the company a loss, said Andy Woerdehoff, safety and health manager for Wells Enterprises.
Junck said the EHS management system Wells Enterprises uses has helped inform company leadership on how to support employees, as well as standardize procedures across plants to better minimize risks of injuries, review incidents and develop effective corrective actions.
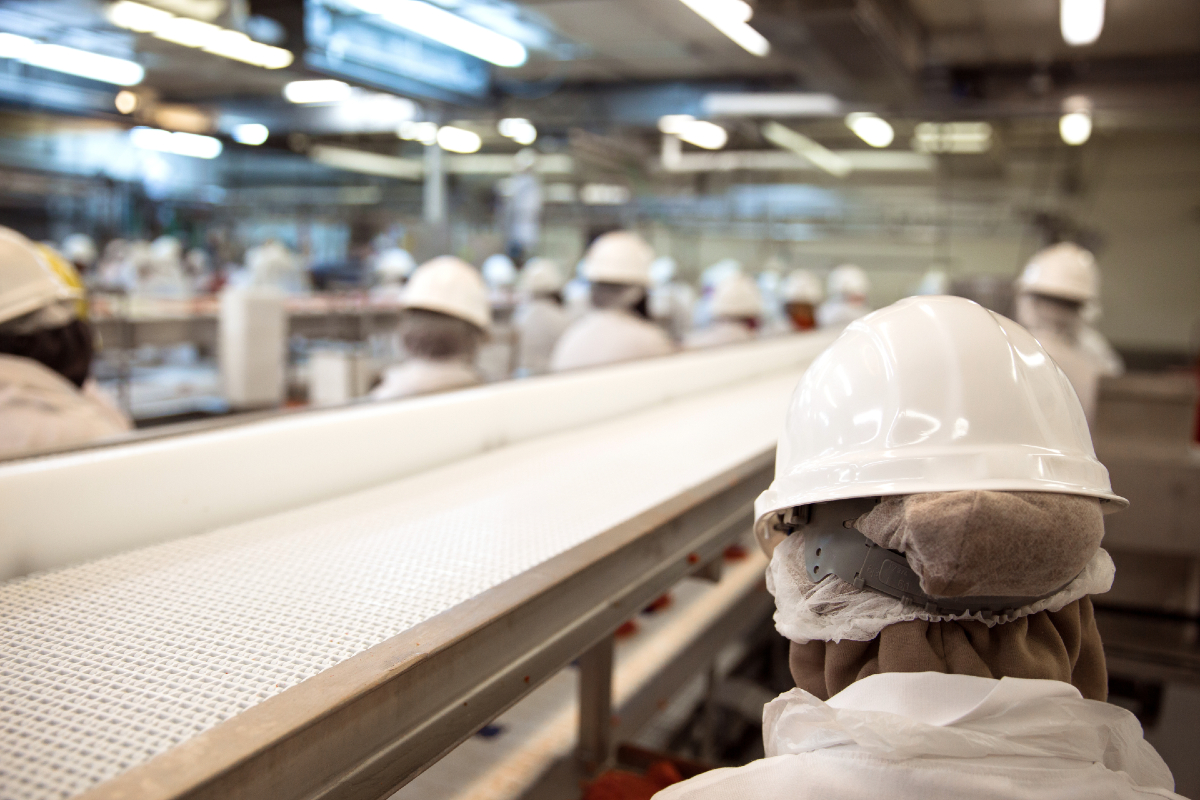
Preventing cyber attacks
Cyber attacks not only can result in significant monetary impacts, but also have the potential to be physically dangerous and destructive to employees and consumers, said Jonathan Braley, operations manager for the Food and Agriculture Information Sharing and Analysis Center. To this end, he said the security of operational technology and industrial control systems should be prioritized.
“There is a lot of machinery dealing with specific pressures, temperatures and refrigeration, so if an attacker were able to get into these industrial control systems and alter some of those levels, you could be dealing with loss of product and the sale of tainted products,” Braley said.
Additionally, attackers causing machines to turn off or on improperly or without notice poses a significant physical risk to workers. Email security is crucial to preventing these attacks, as most attacks begin with a phishing scheme, so Braley said having multifactor authentication is important.
There have been recent incidents in the water sector with some programmable logic controllers being impacted by geo-politically motivated attackers, Braley said. These attacks have disrupted systems, but the water sector has additional safety controls in place that prevented these disruptions from causing widespread concerns regarding water safety.
The possibility of similar threats should be top of mind for dairy processors. Additionally, keeping the right mindset is essential, but Braley said some companies feel they are too small for an attack.
“Most of the cyber attacks we’re seeing, especially against manufacturing, are opportunistic,” Braley said. “It’s not like a threat actor said, ‘I’m going to go after some dairy companies.’ They are going to scan the web, find anything that’s publicly exposed, and then they’re going to test vulnerabilities against it. So even though you are small, if you have poor security practices, you are probably going to be the one that’s going to get hit.”
Ransomware is one of the biggest threats, and Braley said because the industry relies on just-in-time delivery of products, even small delays can have a significant impact on food delivery. As a result, some ransomware operators have targeted food production knowing they are more likely to pay the ransom to restore operations quickly.
Updating software, using unique passwords and multi-factor authentication, creating backup files, encrypting sensitive files, and network segmentation are all best practices to help prevent ransomware attacks.
Traceability
The risks associated with food safety incidents and cyber security vulnerabilities can be reduced by having the right enterprise resource planning software. Marcel Koks, senior industry and solution strategy director for New York-based Infor, said 70% of companies in the food industry report having experienced some level of cyber attacks, so it’s not a matter of if an incident might occur but rather when an incident will happen.
In the past there was a belief that on premises ERP solutions were more secure, but Koks said companies are increasingly viewing the cloud as more secure, as it offers additional redundancy. The predictive maintenance that well rounded ERP systems enable processors to perform also reduces risks, and more dairy processors are using IoT sensors to monitor and repair equipment before a problem arises and a food safety issue occurs.
Koks said a dairy processor working with Infor uses the company’s solution and machine learning to analyze about 30 parameters to determine the quality of cheese they make with the goal of optimizing yield from raw milk. At the same time, the processor is also increasing the quality of its cheese and reducing the risk of making a lower-quality product. The parameters analyzed include humidity, temperature, acidity, fats, protein content, settings of equipment and more.
“By simply doing that for every production batch, they optimize the output, improve the quality, have more consistent product and lower the risk of bad quality and food safety incidents as well,” Koks said. “This is something no human being can do.”
A person doing such a task could only look at a few parameters at a time, and it would take significantly longer to complete the analysis.
Planning production schedules by hand when that involves tank capacity and flow, and bottling and packaging lines, can also pose risks due to simple human error or the inability to conceptualize the bigger picture of the situation, so Koks said ERP systems like Infor help reduce this risk.
Increasingly having the ability to provide real-time traceability data for food safety purposes also makes such ERP solutions essential to being able to meet more stringent regulatory requirements. Additionally, these systems help ensure safety checks are being completed on schedule, said Mikael Bengtsson, industry and solution strategy director for Infor.
Christchurch, New Zealand-based MADCAP offers a solution to help boost this traceability by collecting data on milk going back to the farm and continuing to its reception at the processing plant. The solution can tie into other ERP systems to provide the whole picture.
Nestle uses MADCAP’s solution and it enables the company to see information including volume, farmer payments and composition of the milk within hours or days, whereas such a report used to take nearly a year to produce, said Tomas Vera, MADCAP’s regional director for Europe and Americas.
“(Processors) can react very quickly to anything that happens at a global level or at a local level … because we’ve connected (the data) to the production batch,” Vera said. “We transfer all the traceability information to whatever production system they have.”
This also reduces the risk of food fraud because it allows processors to know where the truck collected the milk, along with all logistical information, which are important details to establish as fraud can occur during the collection process, Vera said.
As the dairy industry works to become more resilient and ready for the future, implementing and building on such risk mitigation initiatives will be essential.