As the dairy industry continues to evolve, so do the technologies and equipment involved in dairy processing. Leveraging the conveyors and palletizers is critical if operators are looking to maximize plant efficiencies.
The global conveyor systems market was valued at $5.42 billion in 2021 and is projected to grow to $7.76 billion by 2029, at a CAGR of 4.8%, according to Fortune Business Insights.
Conveyor systems
Conveyors are an indispensable component of dairy product production lines, as they help to move products from one stage of the process to the next seamlessly. Conveyors come in various designs, depending on the nature of the dairy product being processed, and they offer numerous benefits, including speed, efficiency and cost-effectiveness.
Situating conveyors that are suitable for the specific operating environment is important. Different needs affect selecting the right conveyor appropriate for the different areas of a dairy plant. In packaging areas, for example, non-sanitary conveyors may be acceptable, but those same conveyors would not be appropriate for handling raw product.
One of the most significant advantages of conveyors in dairy product processing is their speed. These systems can move products quickly and efficiently, ensuring that products are produced within the required timeframe. Moreover, conveyors are highly versatile, as they can be adapted to accommodate different types of dairy products, such as cheese, butter and yogurt.
Keeping dairy products in facilities safe and free of contaminants is a major challenge for processors because of the need to minimize cleaning and maintenance downtime to meet operating demands. The most efficient systems have designs that allow for quick cleaning of spills or buildup.
When dealing with a raw product, conveyors must have a superior hygienic design because it carries a higher food safety risk. Hygienic conveyors include food-grade belting and solid crossbars and supports with no hollow bodies that can harbor bacteria. Ease of cleaning in a dairy processing environment is crucial. When selecting a conveyor system for dairy processing operations, 3-A Sanitary Standards should be considered.
The 7X series of conveyors, also known as the AquaGard and AquaPruf platforms, from Dorner, Hartland, Wis., are designed for fast and effective sanitation and protection from contamination. The sanitary conveyors are engineered to promote hygienic design while meeting the sanitary standards of the Baking Industry Sanitary Standards Committee (BISSC), National Sanitation Foundation (NSF), 3A, USDA and other FDA regulations. These models can be disassembled in less than two minutes without tools for effective sanitation with less downtime, making them 100% accessible for cleaning in seconds.
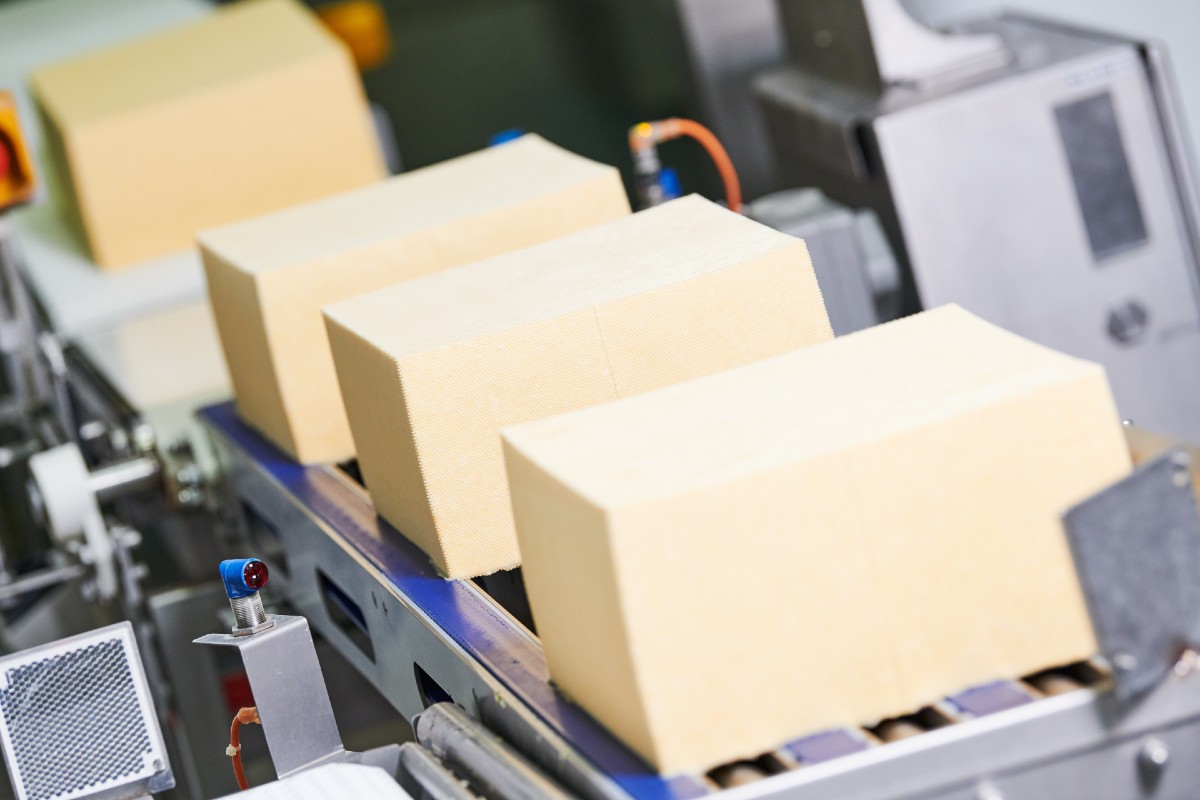
Plastic chain conveyors with stainless steel beams for hygienic requirements from FlexLink Systems Inc., Allentown, Pa., offer the simplicity of a lean interior, reducing the time needed to clean the line and minimizing the risk of cross-contamination. Without crevices for contaminants such as crumbs to fall into and with easy operator access for cleaning, the line starts with high levels of cleanliness that are easy to maintain. Transporting products from primary packaging through to the end of the line, FlexLink provides a clean, simple line layout, following HACCP guidelines.
Conveyors are also designed to minimize product loss, as they ensure that products are transported from one stage to another in a controlled manner. This eliminates the risk of unnecessary spillages, contaminations or product damage, which can result in losses and potentially compromise the quality of the final product.
With conveyors, dairy producers can minimize labor costs by automating the process, reducing the need for a large workforce to move products. This also reduces the risk of injury and human error, further improving the efficiency and quality of the process.
Processors can enhance performance with integrated conveyor lines in which the data collected by sensors on one machine automatically trigger all the necessary adjustments to other machines on the line without human intervention.
Palletizers
The optimal palletizers must also meet processors’ speed, space and budget requirements. While palletizing equipment is not in and of itself new, advancements in technology have made them more efficient, versatile and cost-effective.
Palletizers take on the heavy lifting task of moving finished products from the end of the production line to the shipping area. They are designed to handle various packaging types, including cartons, crates and boxes, making them ideal for dairy product manufacturers who process multiple products.
The palletizer technology has continued to evolve, and some notable advancements include the incorporation of robotic palletizers. These have proven to be even more efficient and cost-effective, as they offer greater precision and speed while reducing the labor costs of using traditional palletizers. The palletizer must fit the floor plan, and handle product efficiently, with an efficient full-pallet transfer. Robotics is likely necessary when palletizing mixed loads. And semi-automatic palletizers can be a wise choice for smaller processors with limited budgets.
Choosing the right palletizers can also minimize the risk of damage to the product during handling and minimize the risk of employee injury. Additionally, palletizers can be programmed to stack products in a particular way, taking into consideration factors such as weight, size and shape, ensuring efficient and safe transportation of the finished products. Bringing multiple lines to a robotic palletizer can also increase the return on investment exponentially.
For such solutions, Delkor, St. Paul, Minn., offers Robotic Palletizers, which can be outfitted with a full array of options including slip sheet/tier sheet, stretch wrapper, pallet dispenser and case conveyance. The company offers single-source solutions for entire packaging lines for seamless integration, simplified operation, and ease of installation. Delkor uses FANUC technology to ensure palletizer systems are turnkey end-of-line systems.
Automating the palletizing operation ensures that products are stacked into secure palletloads that perform optimally in transport and storage.
The Model 72A Palletizer from A-B-C Packaging Machine Corporation, Tarpon Springs, Fla., offers a low-level design, which is easy to install and maintain. The palletizer accepts cases from low- or high-level infeed palletizing and has PLC control, which provides ease-of-operation. This low-level palletizer has one-touch control and allows for rapid product changeover. It handles cases, trays, display packs and totes with features for smooth product transfer and load positioning, delivering square pallet loads for efficient transport.
While this palletizer operates at floor level, it accepts cases from any level. The open construction and floor level access points simplify routine maintenance. On-floor operation allows plant personnel to easily monitor palletizer operation.
As technological advancements continue to push the boundaries of technology, it’s essential for dairy product manufacturers to keep up with the latest innovations to stay ahead of the curve.